The min working length | ≥ 80mm |
Min working width | ≥ 70mm |
Board thickness | 10-25mm |
Edging banding tapes thickness | 0.4-1.5mm |
Degree | 45 |
Feeding speed | 11-13-15m/min |
Total power | 14kw |
Air pressure | 0.65Mpa |
Size | 5900*950*1700mm |
Weight | 1600kg |
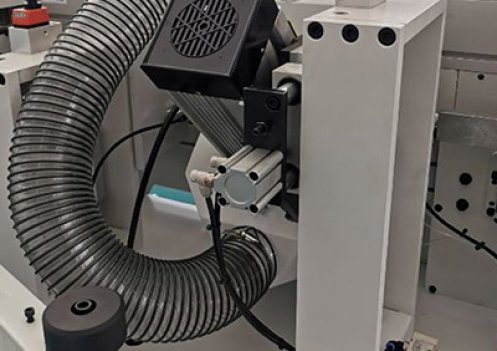
One click lifting function, convenient and fast tool replacement, and straight edge can be directly milled into 45 degree oblique straight edges.
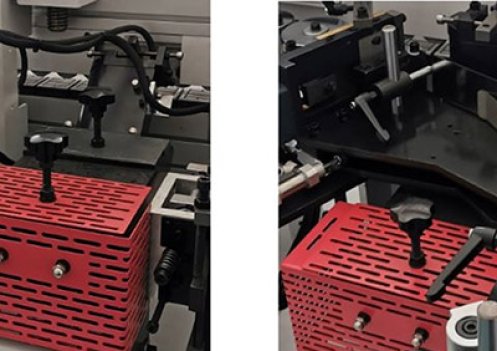
Automatic rubber door control, stable glue coating, uniform external heating/large cycle temperature, PTFE treatment, nonstick gluing pot.
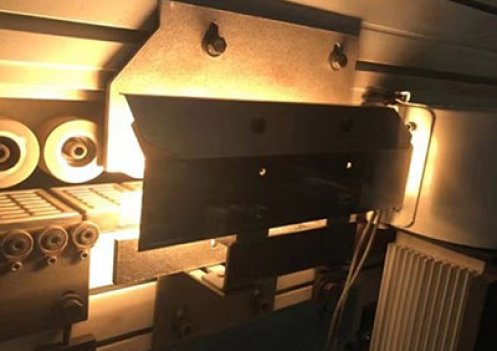
Solve the problem of bad edge sealing caused by low temperature in winter. This device has functions of heating when encountering a board and intermittent heating, effectively reducing energy consumption and production costs.
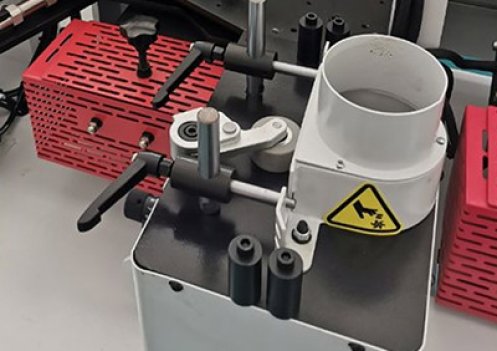
Slot the edge banding tape on the necessary position to ensure a clear edge banded edges and corners. The hand wheel adjusts the depth and height, making it convenient and fast. The front pressure wheel of the edge banding belt is synchronously adjusted with the slotting blade to ensure stable slotting depth.
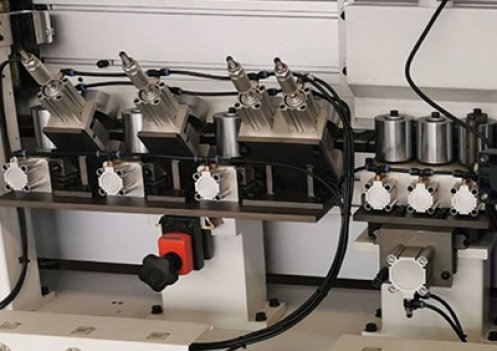
The straight and bevel edges are independently pressed to ensure that the edge banding tape is firmly attached. The pressing wheel is equipped with a scraping function to scrape off excess glue.
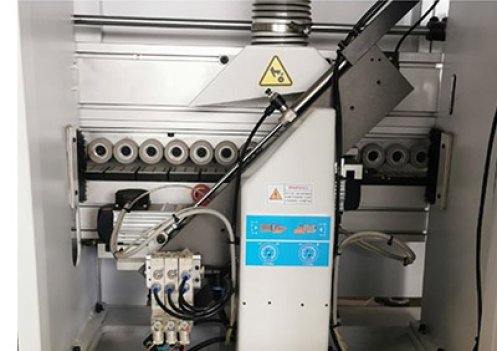
Composed of front end and rear end cutting, it automatically tracks and quickly cuts the remaining material at the front and rear ends with a high-speed motor, ensuring a smooth and even cutting surface.
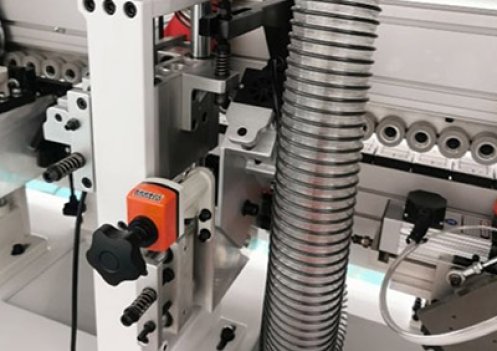
The edge trimming function ensures that the upper and lower edges of the edge banding tap are flush with the upper and lower surfaces of the wooden board, and can be finely trimmed to the desired curvature according to needs, resulting in better edge banding effect.
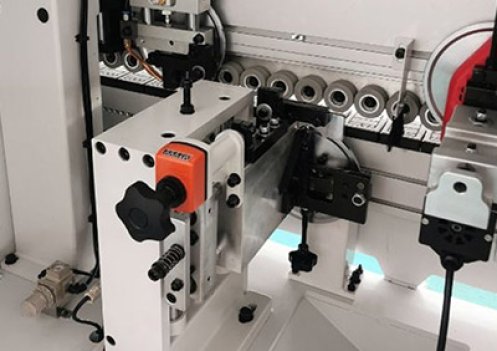
Scrape off any ripple marks generated during the edge banding process to ensure smooth and even edges and surrounding areas of the board.
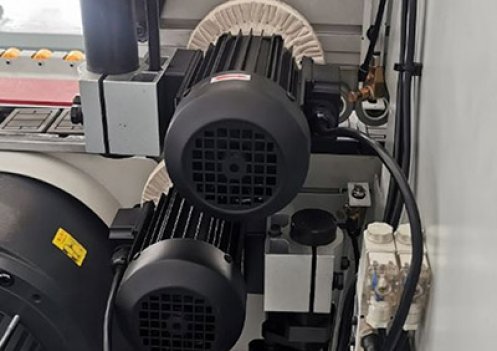
Polish the banded edges of the board and use a cotton polishing wheel to clean the processed board, making it cleaner and smoother after edge banding.